In various industries that rely on pneumatic systems, ensuring smooth and efficient air flow is of utmost importance. This is where air check valves come into play, serving as critical components that enable the proper functioning of pneumatic equipment. From manufacturing plants to automotive assembly lines, these valves play a vital role in maintaining pressure, preventing backflow, and ensuring uninterrupted operations.
An
air check valve, also known as a one-way valve or a non-return valve, is a mechanical device that allows for the flow of air in one direction only. Its design incorporates a disc or a ball that opens under pressure when air flows in the desired direction, while closing to prevent backflow or reverse air flow. This mechanism ensures that air moves freely in one direction, eliminating the risk of air leakage or disruption to the system.
The primary function of air check valves is to maintain system integrity and efficiency. They prevent backflow, which occurs when air pressure drops or reverses direction, potentially causing malfunctions or damage to pneumatic equipment. By allowing air to flow in only one direction, these valves protect against potential system failure, ensuring consistent and reliable performance.
Air check valves come in various types to cater to the needs of different industries and applications. The most common types include spring-loaded check valves, swing check valves, and ball check valves. Each type offers specific features and advantages, allowing users to choose the most suitable valve for their particular pneumatic system requirements.
One key advantage of air check valves is their simplicity and ease of installation. These valves are typically lightweight, compact, and designed to be user-friendly, making them easy to incorporate into existing systems. Their straightforward construction reduces the complexity of installation and minimizes potential downtime during setup or maintenance.
Furthermore, air check valves contribute to overall system efficiency. By preventing backflow and maintaining proper air pressure, these valves allow pneumatic systems to operate at optimal levels. They help regulate airflow, reducing energy waste and ensuring that equipment functions smoothly and consistently. This efficiency translates into cost savings and increased productivity, making air check valves a valuable investment for industries that depend on pneumatic systems.
Another advantage of air check valves is their versatility in handling a wide range of air flow rates, pressures, and temperatures. From low-pressure systems to high-pressure applications, these valves can be selected and customized to meet specific requirements. Additionally, air check valves are designed to withstand various environmental conditions, including extreme temperatures, chemical exposure, and abrasive environments, ensuring long-term reliability and durability.
In conclusion, air check valves are essential components in pneumatic systems, ensuring efficient and reliable air flow. By preventing backflow and maintaining proper pressure, these valves contribute to the smooth operation of various industries, from manufacturing and automotive to pharmaceutical and food processing. Their simplicity, ease of installation, and versatility make them indispensable tools for maintaining system integrity, reducing energy consumption, and enhancing overall productivity. Whether it's controlling air pressure in a production line or regulating air flow in critical pneumatic equipment, air check valves play a crucial role in keeping operations running smoothly and efficiently.
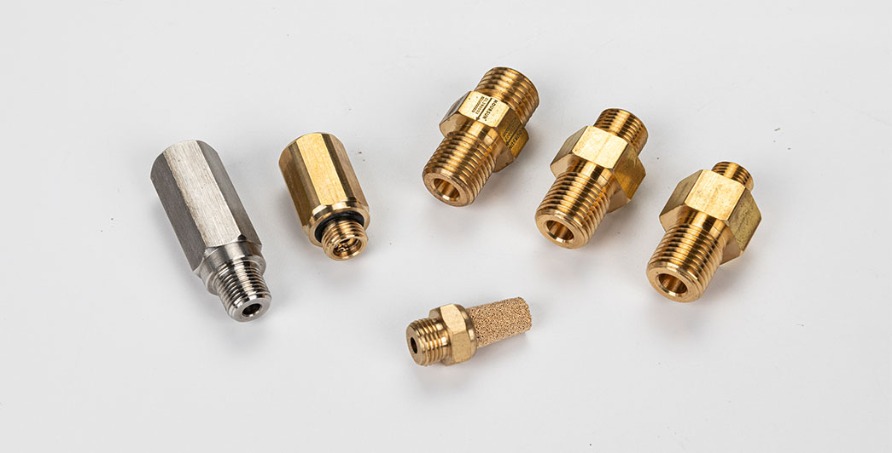